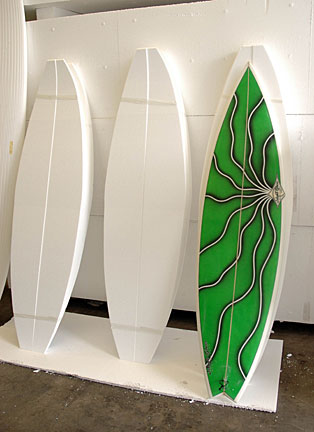
COURTESY OF PACIFIC ALLIED PRODUCTS LTD.
Two of Pacific Allied Products' surfboard core blanks, left, sit next to a finished expanded polystyrene surfboard built by Bryan Caldwell of Island Glass Surfboards.
|
|
Changing surfboard market energizes Kapolei firm
TWO MONTHS AGO, Kapolei-based manufacturer Pacific Allied Products Ltd. was involved in virtually every kind of plastic foam except the business of making surfboard blanks.
But that all changed in mid-December when Laguna Niguel, Calif.-based Clark Foam, the supplier of 80 percent of the world's foam blanks, abruptly shut down.
The closure of Clark Foam due to environmental and fire safety violations, as well as legal challenges, left a large ding in the industry that uses the foam blanks for shaping surfboards.
Industry observers said Clark Foam's departure would increase the cost of buying and making surfboards, as well as create an inventory shortage.
Enter Pacific Allied Products, which makes expanded polystyrene (EPS) core blanks for sailboard manufacturers, as well as foam coolers, packaging peanuts, commercial roofing, insulated concrete forms and other construction-related items.
"Clark had such a hold on the market, by reputation, that they would pretty much undercut anyone who got into the business," said Mike Bilby, EPS division manager of Pacific Allied Products. "We had been making sailboard blanks for a number of years, but we had never got into the local surfboard market until we read about Clark Foam in the papers and noticed a lot of shapers potentially going out of business and running out of product."
Pacific Allied Products, which saw a market opportunity and a chance to fill the void, jumped into the fray in mid-December. He said the company can make up to 500 blanks a month, and is doing about half of that now.
Randy Rarick, a well-known Sunset Beach surfboard shaper and the director of the Triple Crown of Surfing, said 95 percent of surfers are still using polyurethane because it is what shapers are used to. He said the other 5 percent of shapers use epoxy-based EPS and other foams.
EPS is a type of plastic that when heated expands into foam. The foam is then glassed with epoxy resin, which is harder to work with than the polyester resin that is used for polyurethane foam, Rarick said.
"Polyurethane glassed with polyester resin has been the standard for 40 years, and the bulk of glassers in Hawaii are used to working with it," Rarick said. "It's super-easy to work with and not that hard to learn.
"EPS foam is lighter and has better flotation and has to be glassed with epoxy resin. It's harder to work with, and even though the EPS foam is environmentally friendly, the epoxy resin is a little more toxic to work with. That's why most glassers or finishers don't like to work with them."
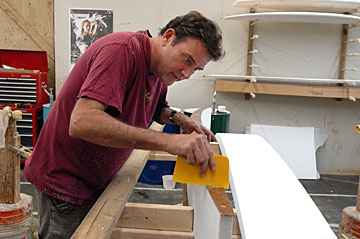
COURTESY OF PACIFIC ALLIED PRODUCTS LTD.
Carl Schaper of Schaper Hawaii adds glue to the stringer that will be sandwiched between two surfboard core blanks for added strength.
|
|
But Clark Foam's demise has given EPS foam manufacturers new life.
"I've been in the surfboard business for more than 14 years, and EPS foam is stronger and much easier to work with compared to other products," said Bryan Caldwell, owner of Island Glass Surfboards. "Surfers will notice a big difference in the flexibility of the board, which increases performance in the ocean."
Still, EPS foam manufacturers face obstacles.
Walker Foam, a Southern California-based rival of Clark Foam, had 5 percent of the market and is now trying to ramp up, Rarick said. Walker went from making 200 blanks a week to 1,000 a day, he added.
Other polyurethane foam providers from Argentina, South Africa, Brazil, Australia and China are trying to grab their market share as well.
So far, the cost of buying surfboards and the materials to make them has risen only about 15 percent so far, Rarick said, because of the inventory left over when Clark Foam went out of business.
Fiberglass Hawaii, which supplies the raw material to make surfboards, bought the inventory from Clark Foam's warehouse in Wahiawa and has been able to meet demand for the polyurethane blanks.
Louis Melton, sales and marketing manager for Fiberglass Hawaii, said that since Clark Foam closed, the demand for EPS foam has increased about 5 percent at the company.
Said Rarick: "I think what the closing of Clark Foam has done is open up the ability to try new technologies, including EPS along with others. Polyurethane and polyester resin is really an archaic 40-year-old technology. A lot of guys are welcoming this change because it forces guys to try newer stuff."