Steel-ing the boom
Hawaii's burgeoning construction
industry sees its profits threatened
by the rapidly rising cost of steel
When Oahu's cement worker strike was resolved earlier this month, Hawaii construction firms breathed a sigh of relief that a key building ingredient would once again be available.
But even before the cement began to flow again, another costly supply headache already had appeared.
A spike in world steel prices over the last few months is hammering local contractors, who say steel costs will severely crimp earnings this year and ultimately will make homes and public construction projects more expensive.
"We're really taking it in the shorts. It's scary," said Ronald Fujikawa, president of Associated Steel Workers Ltd., which is building the Koolani and Hokua high-rises in Kakaako. "I'm not looking forward to seeing our numbers at the end of the year."
The concern is not confined to Hawaii. Construction firms nationwide are grappling with suddenly tight supply and high prices of a range of building materials, from wood to roofing products, due to high demand.
But nothing has risen as suddenly and sharply as steel, a problem that could prove particularly acute in Hawaii, which has the highest percentage of residential steel framing in the country and which is looking to the construction industry to power the economy in the coming years.
The steel used in Hawaii construction comes mainly from U.S. mills, but the price woes can be traced to China. Once a major steel exporter, China is in the midst of an unprecedented building boom and is consuming vast quantities of steel. To keep its own mills humming, China is buying up huge amounts of the raw materials used to make steel, depleting global supply of those ingredients.
As a result, steel -- normally a price-stable commodity -- is fast resembling a precious metal. The price of benchmark for cold rolled steel has rocketed from about $350 per ton in December to just under $800 per ton in April.
"It's been dramatic," said Irving Hirata, president of Mid-Pacific Steel. "It makes your head spin."
The sudden rise has caught contractors off-guard, many of whom won project bids based on steel prices calculated before the recent run-up.
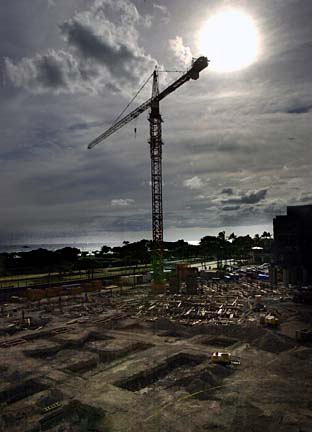
ASSOCIATED PRESS
A large crane towers over the construction site of the Hokua luxury condominiums. Builders say their project budgets underestimated rising steel prices.
|
|
Builders take a risk on supply costs in any project bid. But contractors say steel can account for up to half of the materials expense for some projects, adding that the soaring prices may add as much as 20 percent to 30 percent to the overall cost of some projects.
Construction executives say they have no choice but to swallow the loss themselves on existing projects, but add that home buyers and taxpayers will eventually foot the bill.
"This has been so unusual and rapid, and there is no question that those costs are going to impact the state, owners and developers," said Bill Wilson, president of Hawaiian Dredging and Construction Co. "The contractors are going to have to make that up somewhere."
Steel costs have added a confusing new wrinkle to the competition for project bids. Firms that place bids based on a competitive steel price risk getting burned later if costs rise, as many have already. But if higher prices are anticipated and factored into the bid, a bidder may price himself out of the market.
"You're damned if you do and damned if you don't," said Fujikawa.
Hawaiian Dredging last week put in a bid for the $60 million Hilo Judiciary Building project and was asked along with other bidders to hold the company's bid for six months while the project's funding is worked out. However, Wilson said Hawaiian Dredging's steel-work subcontractors refused to guarantee their prices over such a long, uncertain period.
"We're taking a considerable risk on that one, not only because of the price volatility but because of the long lead time," Wilson said.
Some firms pursuing government projects are pushing to resurrect an arrangement in which contracts oblige the government to pay additional amounts to builders if materials costs rise markedly. The practice was first used during the 1970s oil-shock days as a hedge against soaring prices for asphalt, which is petroleum-based.
Harold Sonemura, the state's acting public works administrator, said contractors have been asking to include such clauses in contracts but the state has turned them away so far.
"I think we're just going to start seeing higher bid prices," he said.
Another hedging option is to stockpile steel in anticipation of higher prices. Fujikawa of Associated Steel Workers said the company normally stockpiles 3,000 tons but has raised that to around 5,000 tons. However, many firms are finding even that difficult. Market supplies are so tight that mainland steel mills are rationing product to buyers.
The resulting shortage of steel has not yet caused any projects to fall behind schedule, Hawaii contractors said, but it has forced builders to do some juggling.
Lance Wilhelm, president of Kiewit Pacific, which does work mainly on large infrastructure projects, said the tight supply is forcing him to adjust work schedules around expected delivery of steel products.
"I've been in this business for 15 years and this is the worst I've ever seen it," he said.
Robert Lee, president of Atlas Steel Corp., a major local importer of steel from the mainland, said he was recently forced to buy South Korean steel for the first time to meet commitments and is still under-stocked. Lee said he expects the high prices and tight supply to continue at least through the end of the year.
That may give an additional boost to the state's spiraling home prices.
Haseko Construction has completed about 1,200 of the 4,850 homes planned for its steel-frame Ocean Pointe project. Adam Sutton, Haseko's vice president, said steel framing will remain the standard for new homes in Hawaii because of its resistance to rot and termites, but home buyers will pay the price if steel costs stay high.
"Ultimately it's the consumer who will feel the pinch," he said.